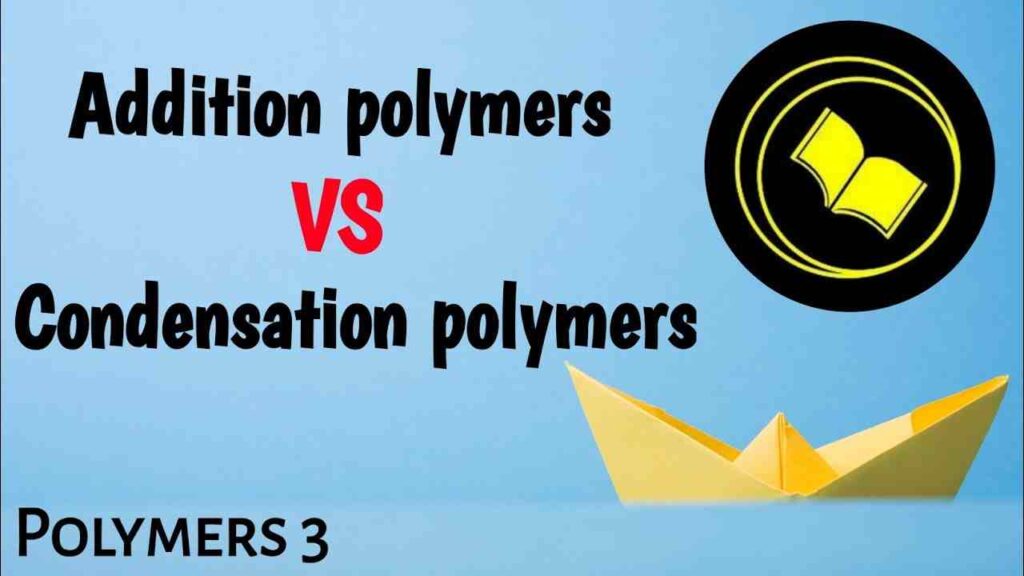
Explore Key 12 Difference between Addition and Condensation Polymerization
Welcome to the fascinating world of polymer chemistry! In this article, we explore the contrasting realms of addition and condensation polymerization, unraveling the 12 Difference between Addition and Condensation Polymerization that give rise to diverse and versatile polymers. Let’s dive in!
Difference between Addition and Condensation Polymerization
Addition and condensation polymerization are two distinct processes that drive the formation of polymers, but they differ significantly in their mechanisms and outcomes. Let’s dive into the twelve key differences that set these two polymerization methods apart.
Type of Reaction: Addition polymerization involves adding monomers one at a time without any byproducts being created. Contrarily, small molecules like water or alcohol are produced as a byproduct of condensation polymerization during the polymerization process.
Monomer Structure: In addition to polymerization, unsaturated compounds, such as alkenes or dienes, typically serve as the monomers. The use of monomers with reactive functional groups, such as carboxyl or amino groups, in condensation polymerization, on the other hand, allows for the formation of covalent bonds.
Reactivity: Since monomers are directly bonded to one another during addition polymerization, no intermediate steps are required, which results in high reactivity. Contrarily, because condensation polymerization reactions involve multiple steps and produce byproducts, they take more time and energy to complete.
Polymer Structure: Since the monomers are simply added to the expanding polymer chain, addition polymerization produces polymers with a linear or branched structure. Condensation polymerization creates repeating unit polymers and frequently causes the formation of cross-linked networks.
Chain Growth: Addition polymerization is carried out via a chain-growth mechanism, in which incoming monomers readily react with the active sites on the growing polymer chain. Contrarily, step-growth is used in condensation polymerization, where the reaction takes place between the functional groups of various monomers, resulting in the formation of covalent bonds.
Initiation: Addition polymerization can begin in a number of ways, including radical, cationic, or anionic initiation, in which free radicals or charged species kick off the polymerization reaction. On the other hand, a catalyst or heat are typically needed to start condensation polymerization.
Molecular Weight: Because monomers are continuously added during addition polymerization, high molecular weight polymers are typically produced. The availability of reactive functional groups on the monomers and the production of byproducts limit the molecular weight of the polymer during condensation polymerization.
Reaction Conditions: Addition polymerization occurs frequently at room temperature and atmospheric pressure and under relatively mild reaction conditions. Contrarily, the byproducts are typically driven off during condensation polymerization, which frequently calls for high temperatures and occasionally vacuum conditions.
Reaction Control: Controlling the reaction is relatively simple because addition polymerization typically occurs quickly and continues until all of the monomers have been used. Due to competing reactions and the presence of byproducts, condensation polymerization can be difficult to control and achieve high molecular weight polymers.
Purity: Since no byproducts are produced during the polymerization process, addition polymers typically have higher levels of purity. The properties of the final polymer may be impacted by residual small molecules in condensation polymers, such as alcohol or water.
Polymer Properties: Because of their regular structure and high molecular weight, addition polymers frequently display more consistent and predictable properties. Condensation polymers can exhibit a wider variety of physical and mechanical properties due to their diverse structural makeup and the potential for cross-linking.
Applications: Addition polymers are widely used in a variety of industries, including packaging, textiles, and electronics, thanks to their special properties. Conversely, condensation polymers are frequently used in industries like adhesives, coatings, and engineering materials because of their advantageous cross-linking and network formation properties.
Addition and condensation polymerization are two distinct processes for creating polymers, each with unique benefits and uses.
Also Read: Explore 10 Key Difference between Flocculated and Deflocculated Suspension